Quality Management
Quality Management
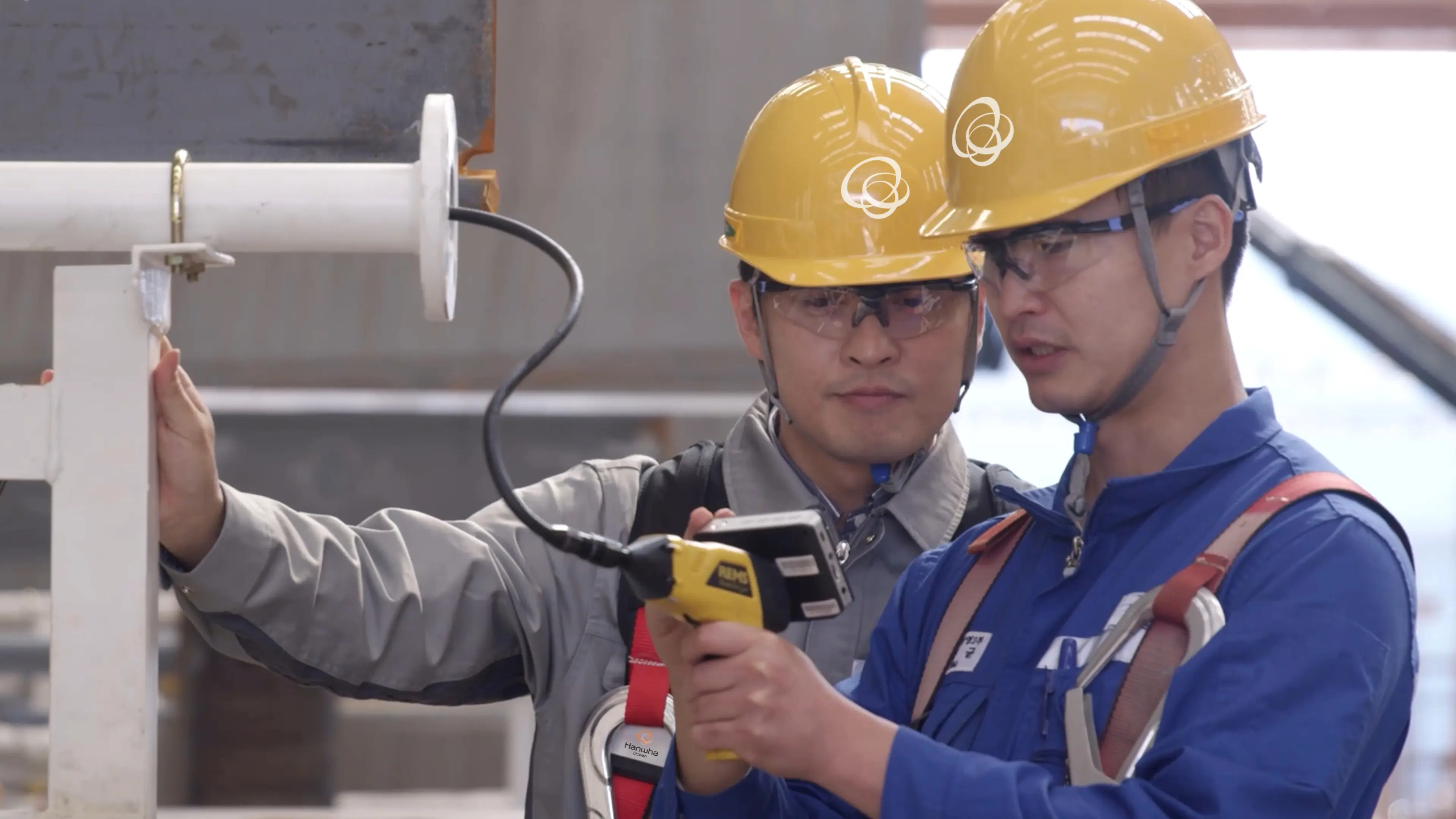
Each year, Hanwha Ocean establishes a quality management policy and shares it with our members. Additionally, we are building a system to manage risks and opportunities by reflecting organizational situations and quality-related demands of stakeholders. Our quality management system is operated based on international standards such as ISO 9001, ISO 29001, and ISO 3834, and we constantly improve our processes through periodic assessments of the quality management system. Furthermore, we strive to achieve high quality by providing satisfactory services to our customers throughout the entire product lifecycle, from ship ordering to delivery and maintenance. Additionally, we regularly monitor the quality and result of assessment of products, services, and technologies through our customer communication channels, and actively provide measures to address customer complaints.
Hanwha Ocean is equipped with an organizational structure dedicated to quality management activities. Accordingly, we offer customer satisfaction services by securing quality based on the performance of roles assigned to each organization.
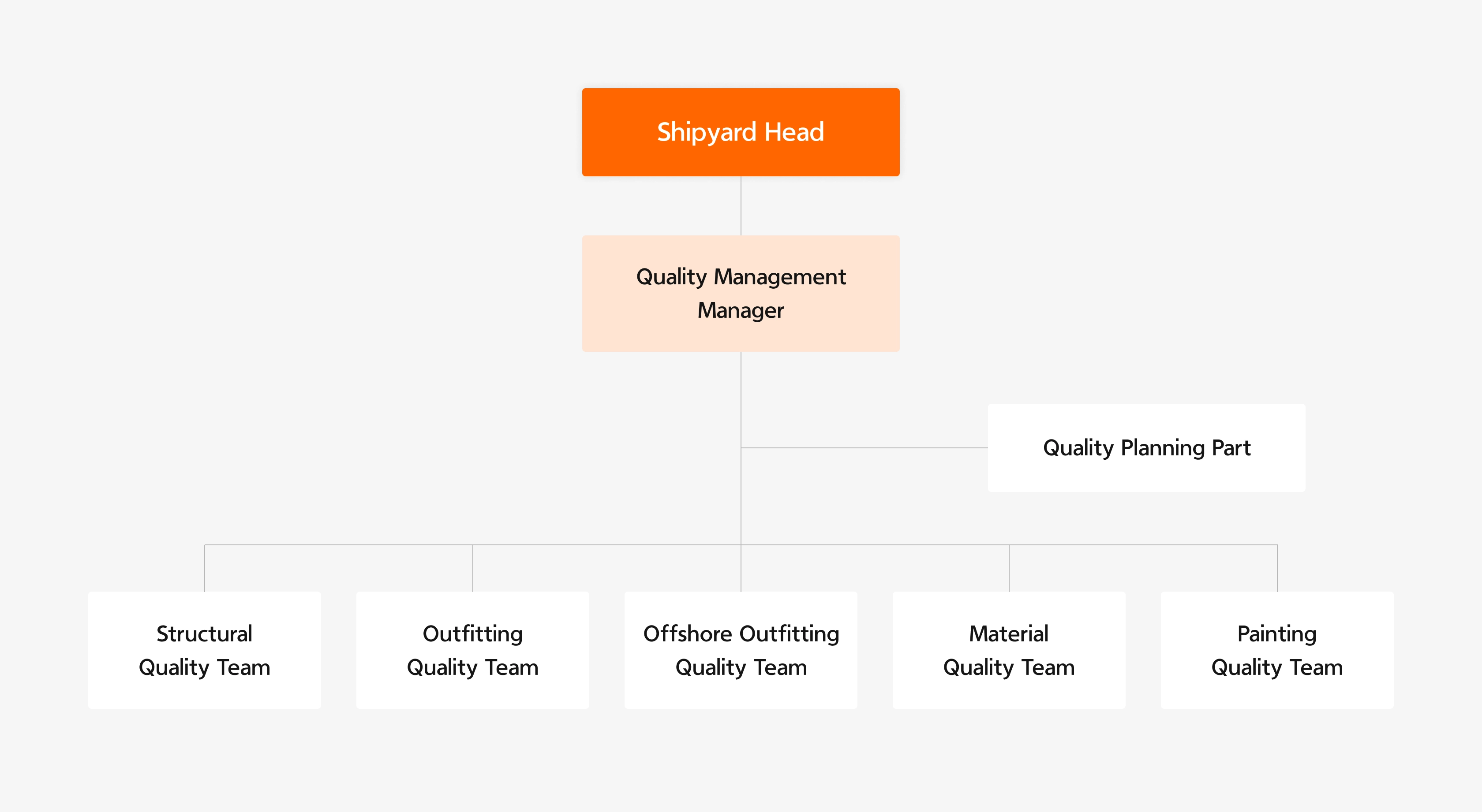
- Shipyard Head
- Quality Management
Manager - Quality Planning Part
- Structural
Quality Team - Outfitting
Quality Team - Offshore Outfitting
Quality Team - Material
Quality Team - Painting
Quality Team
Organization | Roles |
---|---|
Quality planning | Quality planning and improvement, Welder qualifications management, Quality management system certifications management, Non-destructive testing (NDT) quality management |
Structural quality | Ship and offshore structure quality control and inspection (assembly, erection, and external BLK) |
Painting quality | Ship and offshore painting quality control and inspection (assembly, erection, and external BLK) |
Commercial ship outfitting quality | Outfitting quality control and inspection (tubular steel, electrical equipment, commissioning, machinery, CCS, wood outfitting, insulation), Outside cabin and engine casing |
Offshore outfitting quality | Offshore outfitting quality control and inspection (piping, electrical installation, instrumentation, cabin, ironwork), Offshore construction quality management |
Material quality | Equipment quality inspection and management of quality issues, Quality inspection and evaluation of equipment and material suppliers |
Hanwha Ocean strives to build a trusting relationship with our customers by establishing a quality management system centered on improving product quality. Based on this system, we conduct risk assessment and monitoring of product safety and quality, as well as reinforce our responsibilities towards customers, including after-sales service after delivery.
Scope of ISO 9001 certification: Okpo Shipyard, Siheung R&D Campus, Hanwha Ocean Shandong, Seoul Office, Plant Division & Wind Power Division
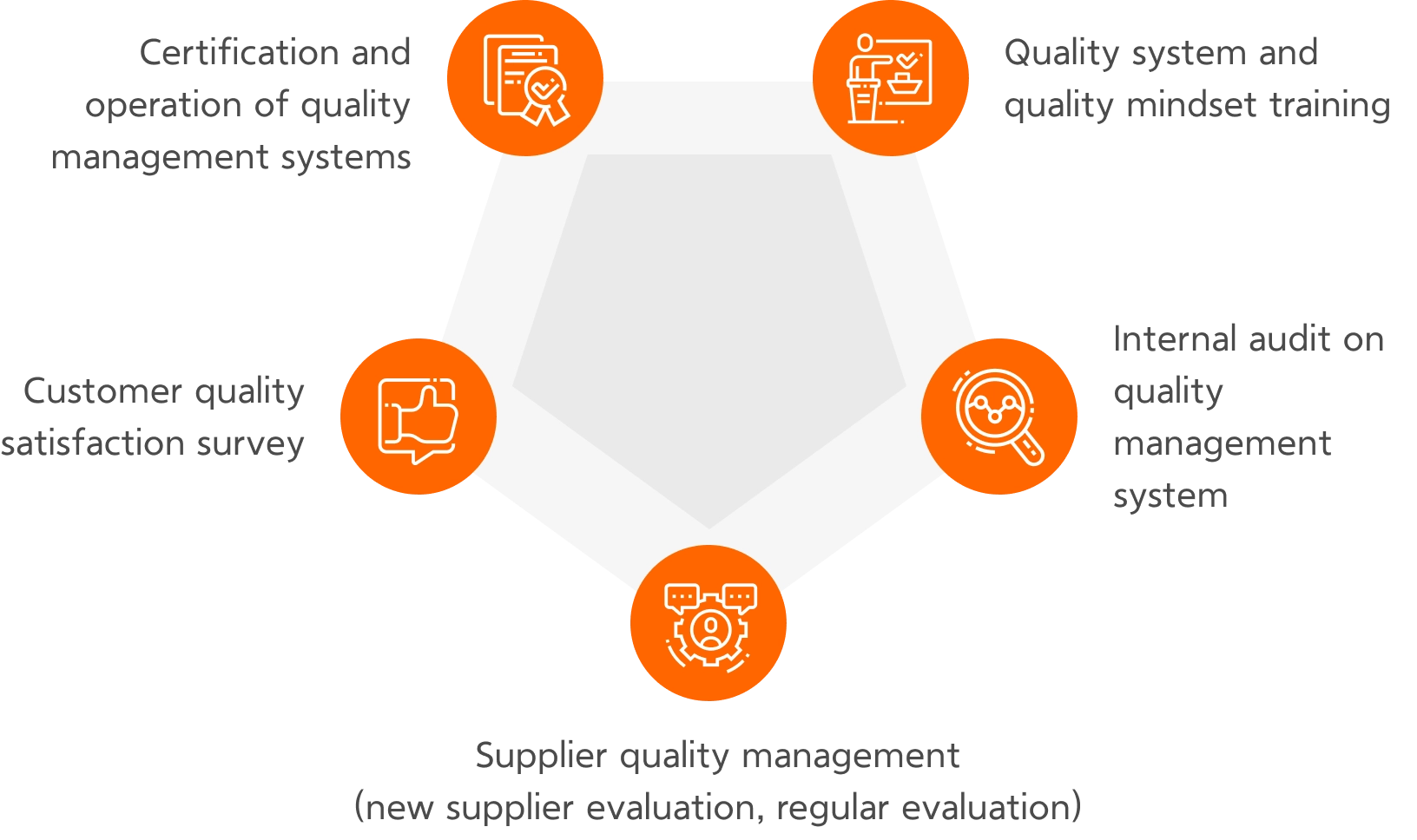
- Certification and operation of quality management systems
- Quality system and quality mindset training
- Customer quality satisfaction survey
- Internal audit on quality management system
- Supplier quality management
(new supplier evaluation, regular evaluation)
-
ISO 9001
-
ISO 29001ISO 3834
Hanwha Ocean selected product safety and responsibilities towards customers as the key issues of quality management for 2023. Accordingly, we took actions by adopting smart quality management approach and listening to customer quality satisfaction.
Key issues | Our response | Key activities in 2023 | Key achievements in 2023 |
---|---|---|---|
|
To improve product safety and quality, we implemented a quality management system ((ISO 9001, ISO 29001, and ISO 3834 certified), conducted risk assessment and monitoring of product safety, and provided after-sales services after delivery. As such, we demonstrate our efforts to build a trusting relationship with our customers. |
|
|
Hanwha Ocean conducts periodic internal and external audits to evaluate the effectiveness of our quality management system, which is constantly improved. The following table details the audits conducted in 2023.
Classification | Target | No. of preventive and corrective actions taken (execution rate) | Anticipated effects |
---|---|---|---|
Internal audit | 24 organizations in total | 79 (100%) | Enhance the process and ensure compatibility through validation of quality system requirements |
External audit | 26 organizations in total | 33 (100%) |
Hanwha Ocean holds quality management meetings to review and assess the targets and performance of quality management indicators for production, design, and procurement. Our key quality management indicators include process inspection retest rate, hit rate, and NDT retest rate, etc.
Classification | Indicator (%) | 2021 | 2022 | 2023 | |||
---|---|---|---|---|---|---|---|
Goal | Performance | Goal | Performance | Goal | Performance | ||
Process inspection | Retest rate | 1.21 | 0.75 | 1.03 | 0.59 | 0.64 | 0.89 |
Hit rate | 97.37 | 98.22 | 97.70 | 98.05 | 98.03 | 97.55 | |
NDT | Retest rate (radiographic test) | 1.58 | 1.71 | 1.58 | 2.25 | 0.99 | 0.99 |
Retest rate (ultrasonic test) | 0.54 | 0.17 | 0.44 | 0.22 | 0.32 | 0.35 |
- * Indicators related to the shipping business (separate indicators for naval and specialty ships)
Hanwha Ocean carries out preventive actions against quality risks through measures such as pre-inspection and claims analysis for preemptive management.
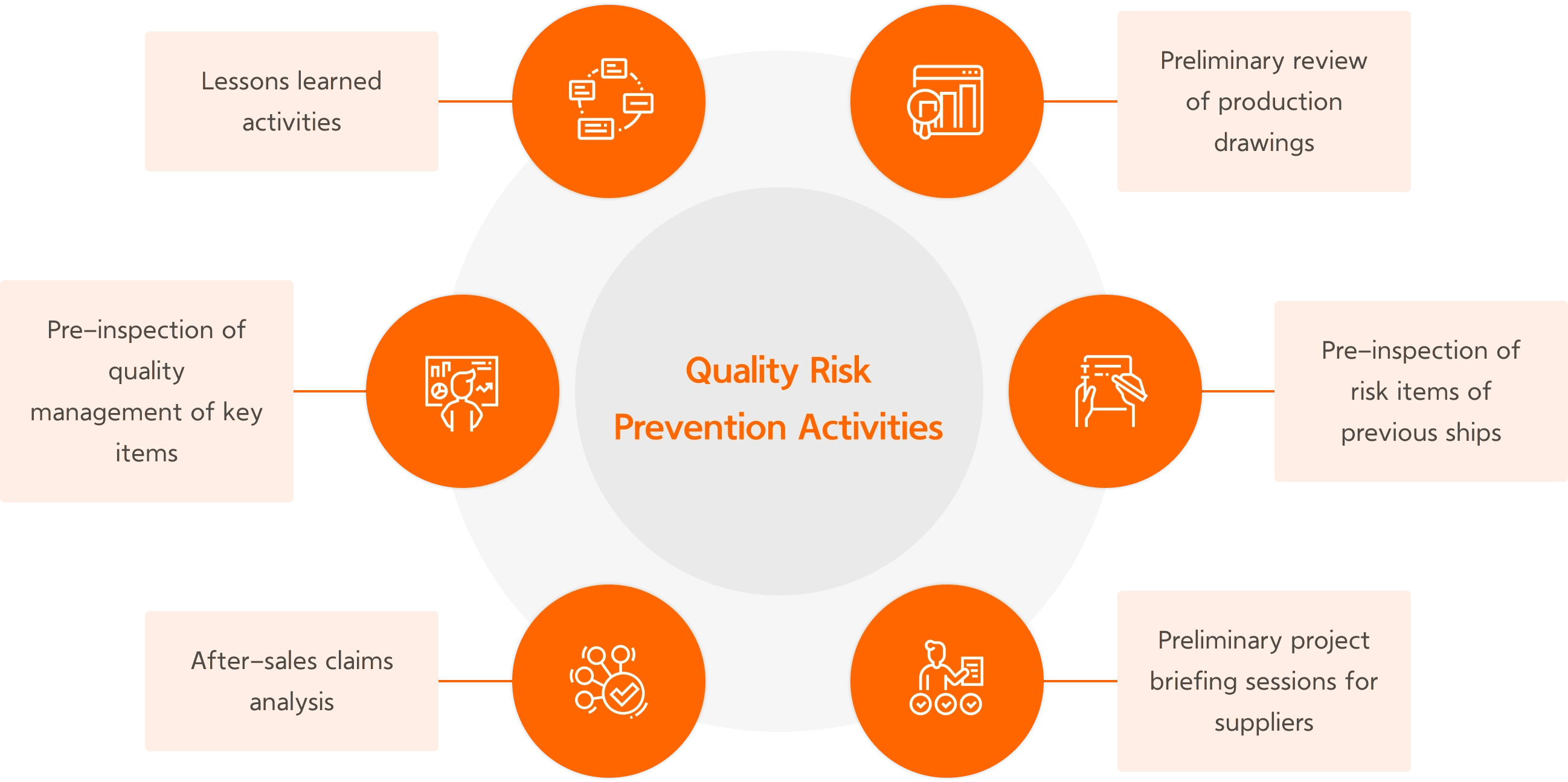
Prevention Activities
- Lessons learned activities
- Pre-inspection of quality management of key items
- After-sales claims analysis
- Preliminary project briefing sessions for suppliers
- Pre-inspection of risk items of previous ships
- Preliminary review of production drawings
Hanwha Ocean selected the following key directions of quality management for 2024: minimizing the cost of failure through quality process innovation, preemptive quality prevention activities and early stabilization of quality, establishing a digital quality management system, securing quality of major equipment and stabilizing quality of suppliers, and creating a culture of responsibility for quality and strengthening quality management capabilities. Based on these initiatives, we work to realize the goal of smart quality management and process improvement to secure both process and quality at the same time.
Key Direction | Key Activities |
---|---|
Minimizing the cost of failure through process innovation |
|
Preemptive quality prevention activities and early stabilization of quality |
|
Establishing a digital quality management system |
|
Securing quality of major equipment and stabilizing quality of suppliers |
|
Creating a culture of responsibility for quality and strengthening quality management capabilities |
|
Hanwha Ocean established a digital quality management system to improve and manage product quality with data-based approach. Thus, we manage all quality management-related processes through the integrated quality management system. Also, we created an environment where inspectors can directly handle all activities related to inspections on-site by linking with the mobile quality system, which was designed to increase production accessibility. To upgrade the existing integrated quality management system, which is our goal for 2024, we are developing detailed activities, including improving input data logic between processes and expanding the scope of remote and delegated inspections. These activities will lead us to advance our system and build an environment for smart quality inspection, resulting in improved work efficiency. Likewise, we will continue to take on challenges and innovate ourselves to become a “great challenger.”
Hanwha Ocean continues to advance and promote improvements by establishing a quality failure cost estimation system to visualize and align the costs incurred due to quality issues. The quality failure cost estimation system allows us to determine investment priorities for quality improvement and estimate the effect of our quality management activities. Leveraging this system, we comprehensively manage costs arising from internal quality issues as well as costs due to customer complaints, constantly pursuing to enhance customer satisfaction and bolster our competitiveness.
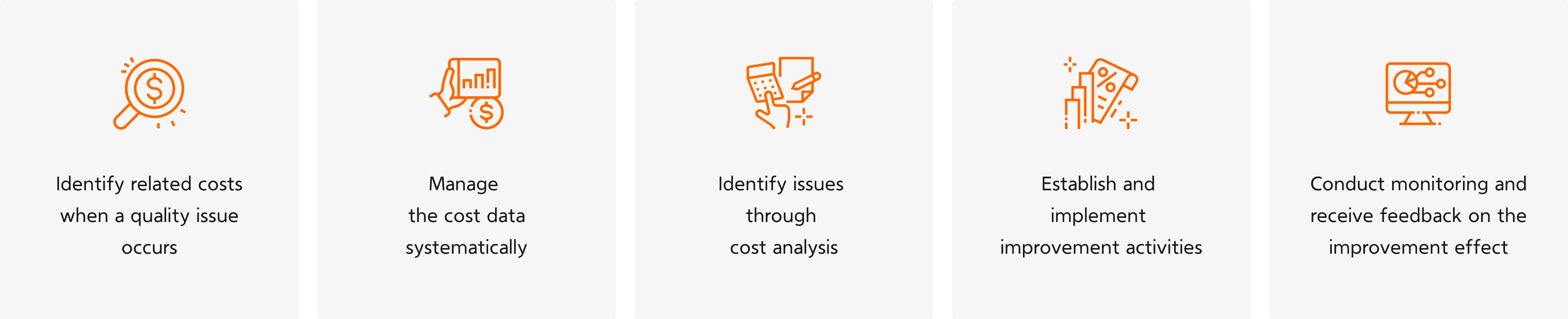
- Identify related costs when a quality issue occurs
- Manage
the cost data systematically - Identify issues
through
cost analysis - Establish and
implement
improvement activities - Conduct monitoring and receive feedback on the improvement effect